DETERGENTE LÍQUIDO Y EN POLVO
Todos los derechos reservados.
®
PROCESO DE PRODUCCIÓN
DETERGENTE EN POLVO




Una de las principales dificultades que surgen en el proceso de fabricación de los detergentes en polvo, es el relacionado con el proceso de mezclado. Se desea un mezclado uniforme de los ingredientes hasta obtener un sólido que solo contenga 10% de agua. El detergente en polvo debe ser soluble en agua y poseer una baja densidad (300-500kg/m3) esto debido a razones comerciales relativas al tamaño del empaque. La presentación más tradicional, consiste de partículas pequeñas (0,5 - 2 mm) y porosas.
Actualmente, existen varios procesos de producción de detergente en polvo, sin embargo, exploraremos sólo uno, correspondiente al del secado por spray drying, esto debido a que es el de mayor uso.
El método consiste en mezclar todos los ingredientes en una suspensión pastosa (slurry) que contiene 30% de agua y luego secar por atomización (spray drying) en una corriente de gases calientes. Es el método más utilizado ya que permite una perfecta homogeneización. Sin embargo el costo energético del secado y el hecho de que ciertas sustancias como los blanqueadores, las enzimas e inclusos ciertos surfactantes, no son estables al calor, han impulsado el desarrollo de otros procesos.

Etapas y Equipos del Proceso
El proceso de elaboración de detergente en polvo puede agruparse en 4 etapas principales:
-
Pre-adición
Esta etapa se trabaja con líquidos, soluciones acuosas y agua, por lo que se le conoce como etapa de mezcla húmeda. Los sólidos están descargados de sus tolvas de almacenamiento por un sistema de dosificación (peso) automática en una línea transportadora de tipo tornillo sin fin, la cual juega también el papel de premezclador. En cuanto a la línea de ingredientes líquidos, es esencialmente semejante, con bombas dosificadoras a la salida de cada tanque. Ambas corrientes entran en un mezclador, el cual es un dispersor de alta velocidad cuyo propósito es eliminar cualquier aglomerado y homogeneizar el slurry.
Reacción de Sulfonación: En la industria de los detergentes es común emplear el dodecilbenceno (DDB) como agente activo. El DDB es sulfonado con el óleum, para formar el respectivo ácido dodecilbencensulfónico (LAS).
La velocidad de reacción es extremadamente rápida y exotérmica. Es necesario mantener la temperatura a 55°C a fin de evitar el exceso de sulfonación y el consiguiente oscurecimiento de la mezcla. Para ello, se emplea un intercambiador alrededor del reactor, el conjunto del reactor y del intercambiador de calor se denomina reactor con camisa. La sulfonación produce una conversión del 96% en menos de un minuto. Las variables a controlar son:
-
Efectividad del agente sulfonante.
-
Relación de agente activo y agente sulfonante.
-
Tiempo de agregado del agente sulfonante.
-
Grado de agitación en la sulfonación.
-
Temperatura y tiempo de agitación de la mezcla reaccionante.
-
Pureza del agente sulfonante.
Actualmente la mayoría de las industrias eliminan la etapa de sulfonación y adquieren por parte de otras industrias químicas el ácido Sulfónico de Dodecilbenceno como materia prima para la producción de los detergentes, como por ejemplo HENKEL.
Reacción de Neutralización: El LAS formado se neutraliza con una solución de sosa caustica, para formar el tensoactivo aniónico, dodecilbencenosulfonato de sodio.
La reacción se efectúa como a continuación se explica: Se deposita la solución de NaOH (20%) y luego se agrega el LAS y se agita a una velocidad tal que la temperatura se mantenga en un rango de 50-55°C. El control de la temperatura es importante para mantener la fluidez de la pasta. Esta reacción es altamente exotérmica, generando de 6 a 8 veces más calor que la reacción de sulfonación. Los equipos empleados para controlar la temperatura en las etapas de sulfonación y neutralización son intercambiadores de calor de flujo circulante.


Pasta Slurry: La masa formada se mezcla con los insumos elegidos para elaborar el detergente. La operación se realiza en tanques de mezcla denominados crutchers (recipientes cilíndricos de base cónica y dispuesta de una chaqueta de calentamiento y un agitador), en donde se forma un lodo pastoso denominado slurry con un contenido de 40-60% de sólidos. En este punto es necesario llevar a cabo un estricto control de condiciones de composición del producto resultante, temperatura (60°C) y pH (10 básico). El slurry pasa luego a un tanque de maduración en el cual "envejece" durante un tiempo de residencia del orden de 20 minutos. El envejecimiento permite la hidratación de ciertas sustancias y una mejor homogeneización. Al salir del madurador, el slurry pasa a través de una bomba homogeneizadora y de un sistema de filtros. Luego se envía a un sistema de bombeo de alta presión (100 atm) que alimenta los atomizadores de la torre de secado.
2. Torre de Absorción
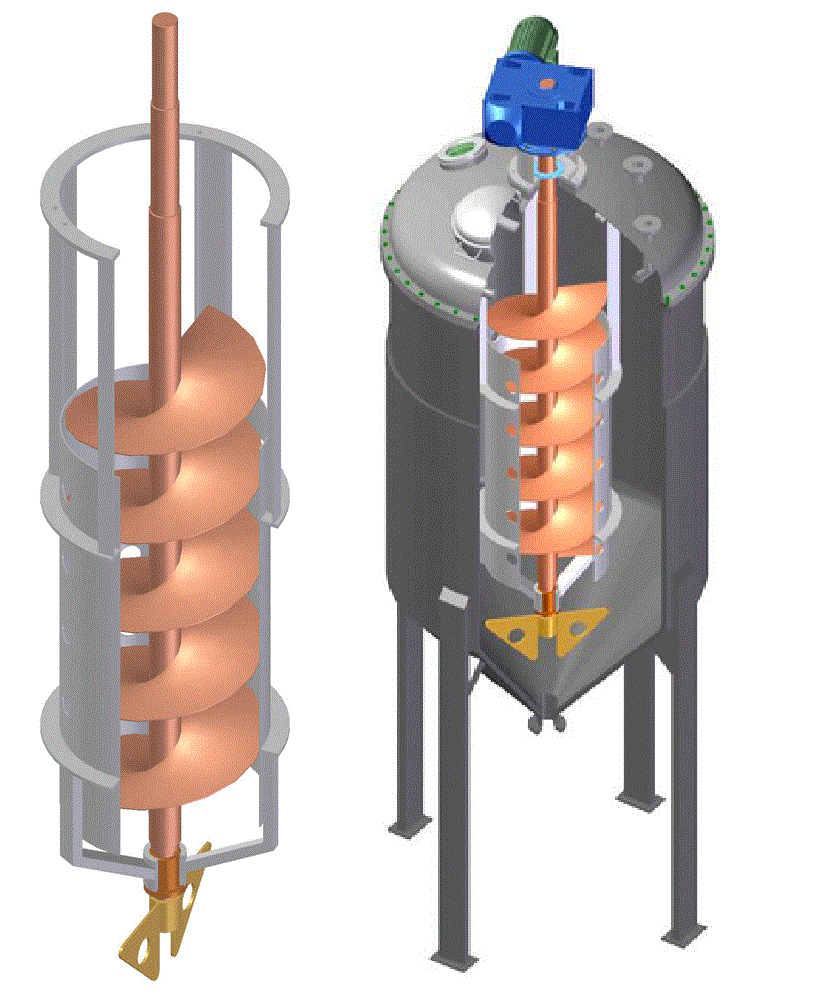

La pasta slurry contiene entre un 30 y 40% de humedad. El producto final deberá contener como un máximo de humedad el 10%, de manera que la pasta se envía a una torre de aspersión para eliminar el porcentaje deseado. El slurry es enviado a un sistema de bombeo de alta presión (100 atm) que alimenta los atomizadores (aprox. 3 mm de diámetro) de la torre de secado. Las partículas son puestas en co-corriente con aire caliente (300°C), o a contracorriente (400°C). Es indispensable que las gotas de slurry no entren en contacto con las paredes, por eso la torre es en general ancha (3-10 m de diámetro). Como siempre existe una pequeña fracción de las gotas que adhieren a las paredes, la torre está provista con un sistema raspador para la limpieza.
El tiempo de contacto varía según los casos entre 10 y 30 segundos. La altura de la torre varía entre 15 y 30 m. El proceso en contracorriente requiere una torre menos alta pero tiene ciertas desventajas. Por un lado, hay mayor arrastre de partículas en los gases; y por otra parte la distribución de tiempo de residencia de las gotas es más amplia, lo que resulta en un porcentaje de partículas demasiadas secas. Por eso se prefiere en general el proceso a co-corriente descendiente.
En la parte cónica inferior de la torre se recolecta el polvo seco (10% de humedad), el cual se envía a una tolva de almacenamiento mediante un transporte por cinta y ascensor de aire, lo cual lo enfría.Los gases que salen de la torre arrastran el polvillo fino, que es indeseable en el producto comercial. Este polvillo se separa en un sistema de ciclones, ajustados con mangas de alta resistencia a la temperatura, y se vuelve a mezclar con el slurry en su etapa de preparación. Los gases que se envían a la atmósfera pasan en general por un sistema de despojamientopara eliminar los eventuales contaminantes. Tales sistemas son del tipo columna de absorción gas-liquido. El líquido empleado es en general una solución de hidróxido de sodio (eliminación del SO2 proviniendo del gasóleo) y de cloruro de sodio (reducción de espuma). La solución saturada se recicla en el slurry. El aire sale a la atmosfera con un contenido de finos y material particulado por debajo de 5mg/m3. La producción de aire caliente necesario para el secado, se obtiene mediante un horno quemador de gasóleo. Éste está dotado de dispositivos para el control de combustión y de regulación automática de la temperatura del aire caliente. Cerca del generador está situado el ventilador que ha de enviar el aire caliente a la torre, provisto de válvulas de regulación de caudal y enfriamiento.
3. Post Adición
En esta última etapa se realiza la operación de tamizado en que partículas de 0,5 a 1 micras pasan como producto deseado (se recogen en la parte inferior del tamizado) y el resto se deshecha en el mezclador de la pasta slurry. Después de realizar la granulometría se añaden los insumos que no se han añadido a la pasta slurry, porque las altas temperaturas de la torre de secado supondría una desactivación de las propiedades de las sustancias, como por ejemplo, el perfume y enzimas. En este punto se realiza un mezclado de sólidos.
4. Envasado
ALa etapa de envasado es una serie de operaciones unitarias mecánicas para dar un aspecto final al detergente en polvo. El polvo terminado se encuentra almacenado en silos, y es envasado en fundas plásticas de polietileno de alta densidad de 30 micras de espesor mediante maquinas envasadoras.

DETERGENTE LÍQUIDO
Un detergente líquido es un tensioactivo o una mezcla de tensioactivos con propiedades de limpieza "en soluciones diluidas". Estas sustancias son generalmente sulfonatos de alquilobenceno, una familia de compuestos que son similares a jabón, pero que son más solubles en agua dura, esto debido a que el sulfonato polar (de detergentes) es menos probable que el carboxilo polar (de jabón) a unirse con el calcio y otros iones presentes en el agua dura.
Cuando se desea que el detergente sea líquido en lugar de polvo, simplemente se mezcla el detergente en polvo con una solución consistente de agua y otros productos químicos conocidos como solubilizantes. Los solubilizantes ayudan al agua y detergente a mezclarse de manera uniforma y completa.
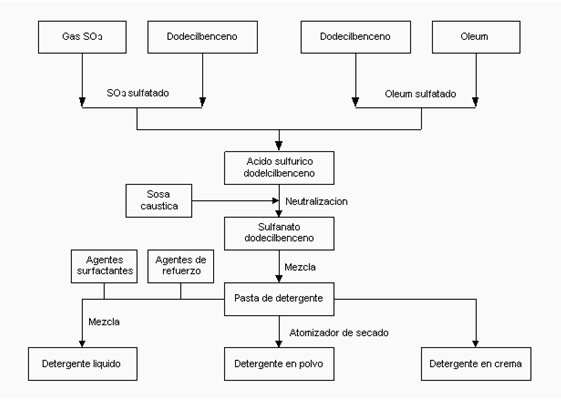